The concept of gear pump is very simple, most basic form is that two of the same size gear in a closely matched housing intermeshing and rotating, the inside of this housing similar to the “8” shape, two gears in the inside, the outer diameter and two sides of the gear closely match with the housing.
The material from the extruder enters the middle of two gears at the suction inlet and fills the space. It moves along the shell with the rotation of the gear and is finally discharged when the two gear mesh.
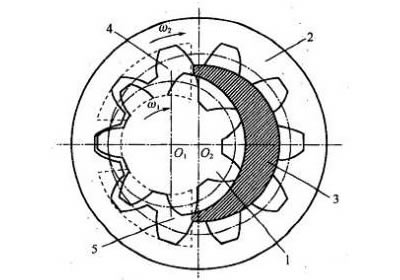
internal gear pump working
Technically, a gear pump is also called a positive displacement device, which is like a piston in a cylinder. When one gearenters the fluid space of another, the liquid is mechanically squeezed out.
Because the liquid is incompressible, the liquid and the gear cannot occupy the same space at the same time, thus, the liquid is excluded.
Due to the continuous meshing of the gear, this phenomenon occurs continuously, thus providing a continuous exclusion at the outlet of the pump. For every turn of the pump, the discharge amount is the same.
As the drive shaft rotates ceaselessly, the pump will discharge the fluid continuously.
The flow rate of the pump is directly related to the speed of the pump.
In fact, there is a small amount of fluid loss in the pump, which makes the operation efficiency of the pump cannot reach 100%, because these fluids are used to lubricate both sides of the bearing and gear, and the pump body can never work without clearance, so the fluid cannot be completely discharged from the outlet, so a small amount of fluid loss is inevitable.
However, the pump can still run well. For most extruded materials, the efficiency can still reach 93% ~ 98%.
For fluid whose viscosity or density varies in the process, the pump will not be affected much.
If there is a damper, such as a strainer or restrictor at the outlet side, the pump pushes the fluid through them.
If the damper changes during operation, that is, if the filter screen becomes dirty, clogged, or if the back pressure of the limiter is raised, the pump will maintain constant flow until it reaches the mechanical limit of the weakest part of the device (usually equipped with a torque limiter).
There is actually a limit to the speed of a pump, which depends largely on the process fluid. If oil is transported, the pump can rotate at a high speed, but this limit is greatly reduced when the fluid is a high-viscosity polymer melt.If the viscosity is higher than 2000cst , kemai pumps suggest choose a internal high-viscosity pump.
It is very important to push the viscous fluid into the two-gearspace on the suction inlet side. If the space is not filled, the pump cannot discharge accurate flow, so PV value (pressure times flow rate) is another limiting factor and a process variable.
As a result of these limitations, gear pump manufacturers will provide a range of products, namely different specifications and discharge rates (the amount of discharge per revolution).
These pumps will be combined with specific application processes to optimize system capacity and price.
The definition and working principle of gear pump the gear pump depends on the working volume change and movement between the pump cylinder and the meshing gear to deliver the liquid or supercharge the rotary pump.
External double gear pump structure:
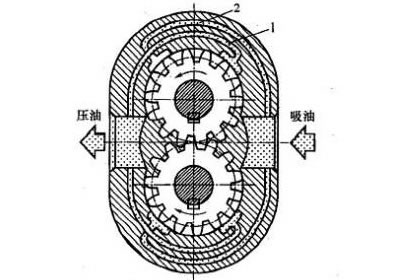
external gear pump working
A pair of intermeshing gears and pump cylinders separate the suction chamber from the discharge chamber.
As the gear turns, the volume between the gear at the disengaging part of the suction cavity side gear gear gradually increases, the pressure decreases, and the liquid enters the gearspace under the action of pressure difference.
As the gears turn, one by one the fluid between the gear is brought out of the chamber.
At this time, the gearspace between the gear of the lateral gear of the cavity is gradually reduced, and the liquid is discharged.
Gear pumps are suitable for conveying lubricated liquids without solids, corrosion-free, and with a wide range of viscosity.
KCB Gear Pump flow up to 300 m/h, pressure up to 3 x 107 pa.
It is usually used as a hydraulic pump and transport of various oil products.
The gear pump structure is simple and compact, easy to manufacture, easy to maintain, and has self-absorption capacity, but the flow rate, pressure pulsation and noise are large.
The gear pump must be equipped with a safety valve to prevent damage to the pump or prime mover due to a cause such as a blockage of the discharge pipe which causes the pump’s outlet pressure to exceed the allowable value.
Please visit more complete gear pumps type and gear pumps products.